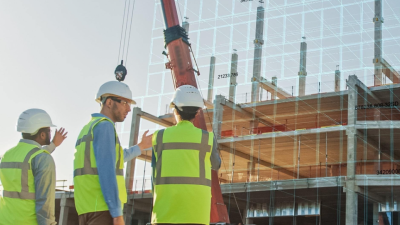
New technologies to improve health and safety performance
Discovering Safety joins forces with Safetytech Accelerator to build a Smarter Regulation Sandbox.
This page is approximately a 7 minute read
This page was published on
For the past four decades, civil aircraft have looked remarkably similar. They have a cylindrical fuselage; a single set of swept back wings mounted below the fuselage; a vertical tail plane (the large fin at the back) with lateral winglets or stabilisers protruding from the rear of the fuselage; and engines mounted below the wings. This has been a remarkably long-lasting design. Its time could soon be up.
Since the beginning of the 21st-century, pressures have risen to reduce pollution and noise and, many believe, these will soon lead to the breaking of this dominant paradigm. Future aircraft design concepts show aircraft tail planes with U -shaped stabilisers replacing the vertical tailplane/stabiliser configurations, narrower wings (which in some designs are swept forward, not back) and engines mounted above the tail stabilisers or integrated into the wings, similar to the first ever commercial airliner, the De Haviland Comet of the 1950s.
And changes won’t just be to design. The materials used to build airliners have been changing over the past decade, with the all-aluminium construction of the late 20th century giving way to a combination of metals and composites.
Perhaps the biggest change will be to how aircraft are powered. The era of the ubiquitous turbojet may be coming to a close. Engines run by electric motors, now in the testing phase, are heralding a new age of short- to medium-range aircraft. Design and propulsion changes go hand in hand; replacing a jet engine with electric motors opens the possibility of lots of small motors rather than two large ones, but brings with it heavy battery storage. Right now, battery weight makes large electric planes impossible, but options that combine batteries with hydrogen fuel cells could offer solutions by 2040.
Engineers working at the sharp end of aircraft manufacture have been driven mostly by the need to reduce weight while maintaining strength, and they see this trend continuing. There are two routes to achieving this. One is replacement of materials with lighter alternatives, such as the aluminium-to-composite trend. The Boeing 787 Dreamliner and the Airbus A350 now fly on wings skinned with carbon fibre-reinforced polymers and only their internal supporting structures are made from metal. Another is embracing new construction methods such as near-net forming and additive manufacture (3D printing). Both present inherent problems that the industry needs to find ways to overcome.
In the UK, Boeing performs a great deal of engineering R&D at the Advanced Manufacturing Research Centre (AMRC), which Boeing founded with the University of Sheffield in 2001. Metallics engineers David Milliken and Joe Fixter work at Boeing Sheffield, the company’s production facility adjacent to the AMRC in Rotherham, and explained that resource efficiency is another driver in technology changes that Boeing is investigating. “At the moment, if you machine a part, there will inevitably be a fair amount of waste metal produced. We really want to make the manufacturing operations more efficient,” said Milliken, a specialist in forming and forging technologies.
Fixter, whose work has centred more around additive manufacturing, believes that these technologies will become more prevalent over the next 20 years. “It could also be very useful for increasing rates of production,” he added. Moreover, he foresees the possibility of expanded use of metals even lighter than aluminium, such as lithium-aluminium alloys. Metals being inherently more recyclable than polymer composites, this could also help reduce the aerospace industry’s impact on
the environment. “If you reuse scrap or recycle from old aircraft, you reduce the amount of virgin metal you have to extract from the ground,” says Milliken.
Additive also suits another trend - digitalisation of manufacturing processes, Fixter said. “We are seeing smarter processes with more sensors, which helps us understand what we can measure in the manufacturing processes and maximise what we can get out of each of the machines. And then, we can look at how we interpret that data and feed it back in to produce high-quality parts more consistently with a much reduced scrappage rate of unsuitable parts.” However, he noted, additive techniques cannot yet meet quality or consistency thresholds for widespread adoption in the commercial aviation industry.
Increasing digitalisation will lead to more demand for process modelling skills within aerospace engineering, Fixter believes, while Milliken noted that expertise in materials properties outside metallurgy will also be in demand.
TWI was among the pioneers of additive manufacturing in the aerospace sector, and Boeing is one of its industrial partners. “We are involved in the TWI’s core research programmes,” Milliken explained. “We have active participation or sight of research into topics such as joining technologies, non-destructive evaluation and coatings. That relationship could develop through making sure that we follow on from some of these research areas when the projects have finished. There could also be more opportunities as Boeing expands its operations in the UK. We’ve grown to 2,600 employees today.” Fixter added: “The main development that we’d want to see is in taking some of the good ideas that we see in the core research programmes and progressing them into industry.”
What will all this mean over the next 20 years? For the individual passenger, perhaps not much. Fliers will likely still travel to airports to be whisked around the world, thought the whisking will be done on quieter, cleaner and faster jets. But the industry, and those supporting it, is likely to see big shifts.
Boeing recently released its annual Commercial Market Outlook. Even factoring in the downturn caused by Covid, Boeing predicts market fundamentals will drive demand through 2040 for more than 43,500 new aeroplanes. The global commercial fleet will surpass 49,000 aeroplanes by 2040.
Another trend that has been seen in aerospace over the past decade has been a shift away from using very large airliners to travel to major hub airports and towards ‘point-to-point’ travel between smaller regional airports in medium-range aircraft, which has seen the retirement of the largest long haul workhorses. Whether this translates to growth in construction of regional airports is yet to be seen. How aerospace recovers from its 18-month hiatus enforced by the coronavirus pandemic will shape short term investment in airport infrastructure, and – since airports are intended to last – decisions now will have far reaching impacts on the future geographic shape of the industry.
This last point is a big unknown in the aerospace industry, and aircraft makers are reluctant to discuss it. However, as the world has adjusted to communicating via video calls rather than in-person meetings since early 2020, many observers think it likely that even large corporations will seize the opportunity to economise by reducing the number of flights they book for employees.
In a report issued in April 2021, management consultancy McKinsey and Co estimated that business travel will only recover to 80% of pre-pandemic levels by 2024. The report points out that after the 9/11 terrorist attacks, leisure trips bounced back almost immediately. After the financial crisis, they recovered in three years. But business trips had not fully recovered to pre-financial crisis levels when covid-19 hit. This will lead to a need for new strategies for airlines, McKinsey says, with ticket prices likely to rise and larger aircraft flying less frequently, and serving routes from major hubs to smaller cities.
However the industry realigns itself, the one thing that seems certain is the move towards greener aircraft, and that brings long term implications on supply chains. If aircraft embrace fuel cells and batteries, that will increase demand for many already oversubscribed metals.
If, as seems likely, it moves to non-fossil fuels, that could have a big impact on the way the world looks, as these fuels must be produced using clean energy to be viable. Windfarms may proliferate offshore to produce hydrogen. Swiss company Synhelion is developing synthetic fuels with solar power, using vast fields of mirrors to generate the energy – could we see North African, Middle Eastern and American oil fields replaced with solar fields? As discussed elsewhere in this report, fusion could eventually be to create clean fuels on large scales.
Aerospace may be one of the last industries to fully decarbonise. But as it does, thanks to innovative designs of both engines and planes themselves, it may help finally end our reliance on oil, and in doing so, reshape geopolitics.