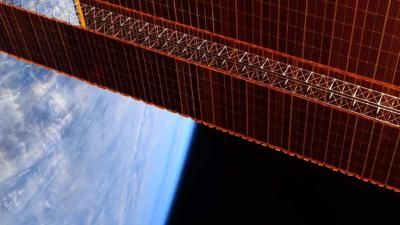
Reaction Engines on the space economy
If we are to continue thriving as a connected, energy-hungry planet, we will eventually need to look beyond our own atmosphere.
This page is approximately a 6 minute read
This page was published on
Orbiting a point 323,000 km above the Earth, where its gravity is cancelled out by the Moon’s, the international Deep Space Gateway Station glitters in the sunlight. Originally designed as a staging post for crewed lunar missions, in the 2040s it is now taking on a different role – a factory for constructing satellites. Robotic machines whirr busily in the velvet blackness, extruding composite spars and sheets, welding components and placing payload into the structures.
Thousands of miles away, a spark rises from the distant Earth: an automated supply capsule carrying raw materials and boxes of electronics for the next set of satellites. As each new satellite is completed, it detaches and small electric thrusters direct them towards their designated orbit around the planet.
Fast-forward another 30 years to the last quarter of this century. In a conical capsule, attached to the gateway, humans flick switches. A low hum marks the start up of their nuclear fusion propulsion system: a scrap of star-stuff, confined within an invisible bottle. Its crew face a long flight. Their predecessors tested the in-flight life-support system on the one month journey to Mars, but these astronauts are headed further - on a one-year cruise to Europa, where they will set up the research station to study the aquatic life discovered below its icy crust decades before.
It’s science fiction now, but everything in the preceding paragraphs (except, perhaps, the swimming Europans) is firmly on the agenda of space agencies and private space concerns for the coming decades.
It’s easy to underestimate the importance of space as a platform for infrastructure, but even now in 2021 most of us depend more on assets in space than we realise. Satellites enable our communication around the world. They help us to navigate in our cars. They make it possible to monitor the weather and predict how it will change. Increasingly, they are part of countries’ defence. In the next few years, they will increasingly be used to identify locations at risk of climate change and to help farmers maximise their crop yields. Earth observation is finding new commercial applications at an accelerating rate, and the desire for humanity to explore the solar system is unlikely to wither.
At the sharp end of space exploration, Tommaso Ghidini, head of the Structures, Mechanisms and Materials Division of the European Space Agency, says that “as space becomes increasingly important, we will need to start establishing the infrastructure to build and maintain all or the equipment we need in space.. Then, maybe 20 or more years out – we are going to be using space as a resource, not just for science and observation, but for living in space.”
Out-of-Earth manufacturing, as we call it, is a very active program at ESA. TWI was instrumental in this – the support we got from the Institute and the collaboration helped us create the Advanced Manufacturing Cross-Cutting Initiative. Through this, we are taking advanced Manufacturing technologies from general industry into space, qualifying those to very stringent requirements which space imposes, and then spinning them back out into non-space industrial sectors, but this time at a much larger scale and hence with a greater return on investment,” says Ghidini.
As part of this initiative, ESA is looking at assembling new Earth observation satellites with large reflectors in space. “We are looking at in situ resource utilisation, systematic recycling, and all of these manufacturing processes. In my opinion, by 2040, this will probably be happening.”
An advantage of off-planet manufacturing is that it removes the main limitation of current space missions – the volume and mass that can be launched. “By changing completely the approach and having assembly and manufacturing capabilities on orbit or beyond, we can make much larger satellites in space,” Ghidini says.
“And this doesn’t just mean assembling components that have been lifted out of Earth’s gravity well. “The idea would be to have manufacturing capabilities directly on orbit. That would mean that the spacecraft would not have to survive the rigours of launch, so super-expensive materials like titanium, which you need to meet the conditions of launch, could be replaced by polymers. You’re building, deploying and using the spacecraft entirely in zero G so you no longer have the structural requirements of an Earth-launched system.”
“I think it would be a hybrid approach in the medium-term – maybe propulsion systems and electronics would still need to be manufactured on Earth and launched to the platform for assembly – but by 2040, the proportion of the manufacturing that could be done in space would be significantly larger than it is today.”
ESA has taken major steps towards this goal with the establishment of a project called PERIOD (PERASPERA In-Orbit Demonstration) in March 2021, aiming to develop and launch a demonstrator satellite assembly and manufacture platform in space by 2023. This project will be handled by Airbus, which in July successfully established Europe’s first fully-automated solar array production facility at Ottobrunn in Germany. Here, 17 robots (all named after stars in the Milky Way) perform 60 production steps to assemble solar cells, incorporate them into arrays and prepare them for attachment to spacecraft. In the immediate term, this facility has halved lead times for these components and reduced their cost, but it is easy to see how such technology could be used off-planet.
Ghidini is also keen to stress the growing importance of cleaning up space: removing non-operational satellites from orbit, and is very enthusiastic about the mission CLEARSPACE-1, developed within the frame of the Clean Space initiative and targeting the de-orbiting of a rocket upper stage as a first very important step to demonstrate active debris removal capabilities.
Ghidini also notes that ESA and NASA currently have a vision of potentially establishing a base on the Moon that could support mining for raw materials for use in manufacturing. Preparation is already underway, with aluminium, titanium, silica and iron being extracted by the Moon surface, with oxygen produced from the same process. This is opening the way to use Moon dust to extract materials for in-situ manufacturing with 3D printers, and oxygen for the astronauts to breath.
These new satellites, built in orbit, will improve communications, and support research that improves humanity’s understanding of our home planet. “We are already monitoring the 60 variables that influence climate change,” Ghidini said. “And that’s not just about climate change. We now have satellites looking at the built environment, measuring millimetre movements of bridges and other structures to anticipate failures and prevent collapses. They can also help protect us from natural threats such as tsunamis or volcanic eruptions. It is very important that
ESA generates data that are unquestionable. We provide those data to decision-makers who can initiate action to intervene and, for example, start to reverse climate change, repair structures or launch humanitarian rescue missions.”