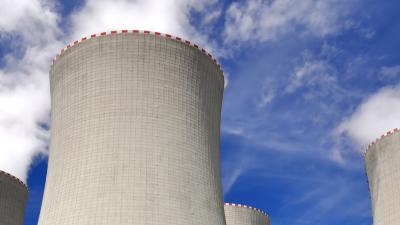
Tokamak Energy on fusion
After a long wait, fusion – the process by which stars derive energy – is now approaching a state of readiness.
This page is approximately a 2 minute read
This page was published on
In a rocket engine, fuel is mixed with an oxidiser, and combusts to generate propulsion. But carrying this oxidiser on board adds a lot of weight. SABRE generates its own oxidiser from the air around it, thanks to a feat of precision engineering.
During flight, air is sucked into the engine. Rapidly slowing air from hypersonic speeds to a standstill creates high compression, heating it to over 1,000oC.
SABRE’s precooler – a system of thousands of tubes that allow coolant to be injected and removed for extremely efficient cooling – rapidly cools the air to ambient temperatures or down to -150oC in 1/20th of a second.
This has two critical effects. The heat extracted from the air powers a compressor via a turbine. The low temperature air feeds into this compressor, creating oxidiser. This is combusted with hydrogen to create propulsion.
This highly efficient system can be built into a lightweight aircraft or spacecraft design. Outside the atmosphere, it switches to a highly efficient rocket mode, which uses stored liquid oxygen in far smaller quantities.
All this is made possible by the design of the precooler, which incorporates thousands of millimetre size tubes, made from hair-width materials, to deliver revolutionary heat management and fully proven to Mach 5 (1,000oC) temperatures. Reaction Engines worked closely with experts from TWI to understand how to join these together to optimise efficiency and ensure no leakage under extremely harsh temperatures and pressures.
“There is a certain satisfaction to realising that access to the vast realm of space is made possible by innovations in how we join together materials at the nano scale”, says Mark Thomas, CEO of Reaction Engines.