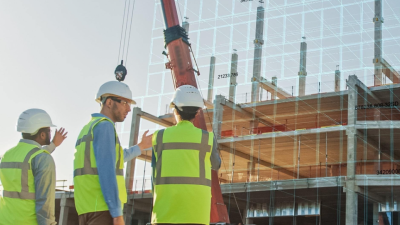
New technologies to improve health and safety performance
Discovering Safety joins forces with Safetytech Accelerator to build a Smarter Regulation Sandbox.
This page is approximately a 5 minute read
This page was published on
Dutch scale-up MX3D is awarded the “Outstanding Development in Welded Fabrication” by the American Welding Society (AWS) for the “MX3D Bridge”, its innovative 3D metal printed bridge for the City of Amsterdam.
Past winners of this prestigious award are the Hoover Dam, the Grand Canyon Skywalk and the New York One World Trade Center, the Mars Curiosity Rover, the PipeLine Under The Ocean (PLUTO), and the Panama Canal.
The MX3D Bridge is the first of its kind and measures 12 metres or 36ft. It was fabricated with MX3D’s proprietary robotic Wire Arc Additive Manufacturing (WAAM) technology, which is 3D metal printing with welding robots controlled by MX3D’s MetalXL workflow. In 2021, the bridge was opened by Queen Maxima of The Netherlands.
The MX3D Bridge was designed by Joris Laarman lab in close collaboration with lead engineer Arup. The project was brought to life thanks to the indispensable support of industry leaders including Autodesk, ArcelorMittal, ABB, Air Liquide, and Lenovo. Additional funding by the Dutch RVO and Lloyd's Register Foundation helped MX3D realise its bold vision for autonomous 3D metal printing of large structures.
The MX3D Bridge showcased the groundbreaking use of Wire Arc Additive Manufacturing (WAAM) technology to 3D-metal print a fully functional, intricate steel bridge. This innovative fabrication technique is based on advanced welding processes. It served as a poster project for the company and the technology. Since the bridge project MX3D has successfully introduced its technology in other demanding industries like Space, Maritime, Nuclear, and Energy.
The Bridge served as an innovative playground allowing for all partners to experiment with new technologies like IOT systems, Digital Twins and 3D printing. It will remain a platform for innovation at its new location, which will be announced shortly.
The American Welding Society Outstanding Achievement Awards recognize remarkable contributions in welding, achievements in historical structures, innovative fabrication techniques, safety practices and technical advancements in multiple categories. The “Outstanding Development in Welded Fabrication” program was established in 1993 and ever since has been a promoter of the science, technology and application of welding, encouraging members to become aware of the metal's heritage and generate public awareness of the importance that metal welding provides to daily life.
“Receiving the ‘AWS Outstanding Development in Welded Fabrication Award’ for the MX3D Bridge is a remarkable honour. This award highlights the innovation, collaboration and perseverance that went into bringing the MX3D Bridge from concept to reality. I am really proud of the close-knit team of partners that pushed the boundaries of what’s possible with welded fabrication,” says Gijs van der Velden, CEO of MX3D.
The MX3D Bridge design was created using generative design and topology optimisation techniques. The combination of these digital design tools with MX3D’s advanced robotic 3D metal printing technology allows for a higher form liberty and significant material reduction. The environmental impact of metal parts manufacturing can thus be improved significantly using WAAM.
MX3D Bridge: a ‘living laboratory’ & smart sensor network feeds ‘digital twin’
As the MX3D Bridge is equipped with a state-of-the-art sensor network, the ‘Smart Bridge’ powered a cutting-edge research project. Innovative in design and technology, the bridge served as a living laboratory. In concert with academic and industry researchers, the City of Amsterdam used the bridge’s data streams to explore the role of IoT systems in the built environment.
Building a complete digital twin of the bridge serves to inspect the current state of the structure, log its use in real-time and enable predictive maintenance. Realising this vision required an extended and intensive collaboration between MX3D, The Alan Turing Institute, Imperial College London, Arup, Autodesk, FORCE Technology, and the University of Twente.
MX3D is the leading industry player with 10 years and over 40,000 kg of experience in advanced robotic metal 3D printing solutions with the Wire Arc Additive Manufacturing (WAAM) process. With a focus on large-scale printing innovations, MX3D delivers cutting-edge metal 3D printing systems to energy, (aero)space, automotive, maritime and manufacturing industries. Our mission is to continuously push the boundaries of robotic 3D metal printing in terms of size, quality, lead time and cost-efficiency.
MX3D’s MetalXL technology and their M-Metal AM Systems print large-scale metal components all over the world. Where its M1 Metal AM System is the optimal system for starting robotic 3D metal printing fast, its MX Metal AM Systems is purposely customised and built for businesses to print specific large-scale and heavy applications. Next to industrial companies and manufacturers, MX3D’s metal AM systems are also used by R&D centres and educational institutes for their ease of use and dedicated end-to-end software MetalXL. Customers include BMW Group (Germany), the US Army (USA), Shimoda Flanges (Japan), CIT SENAI (Brasil) and EMPA (Switzerland).
The company also Prints on Demand. It has one of the largest robotic 3D printing facilities in the world, with its HQ in Amsterdam. MX3D has printed over 40,000 kg of metal parts in various alloys. It can handle prints up to 10.000 Kg, in a variety of alloys like (high strength) steel, stainless steel, duplex, Inconel, aluminium, bronze and more.
The MX3D Bridge project has only been made possible through the close collaboration with partners Autodesk, Heijmans, Joris Laarman Lab and ArcelorMittal and the support of Lead Structural Engineer Arup, The Alan Turing Institute Data Centric Engineering Programme, Lloyd's Register Foundation, Air Liquide, ABB Robotics and Lenovo. Important contributions have been made by: FORCE Technology, HBM, Oerlikon, Faro Technologies, STV, Oerlikon Welding, Mous, and Plymovent. The public partners are TU Delft, Imperial College London, University of Twente, AMS Institute (Amsterdam Institute for Advanced Metropolitan Solutions) and the Municipality of Amsterdam.
For more information about MX3D, click here.