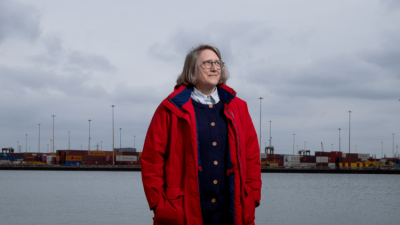
Rewriting Women into Maritime makes London International Shipping Week debut
Rewriting Women into Maritime makes London International Shipping Week debut.
This page is approximately a 3 minute read
This page was published on
Lloyd’s Register Foundation has been working with MX3D to create the world’s first full-sized 3D printed steel bridge, which will carry pedestrians over a canal in Amsterdam. The bridge will be a ‘living laboratory’ which an international collaboration of engineers, data scientists, computer scientists and statisticians will use to improve structural integrity in bridges.
While catastrophic bridge collapses are rare, experts estimate that 12% of the structures we walk and drive over every day are structurally unsound.
Our Netherlands-based partners, MX3D, are developing the 12m ‘smart bridge’ to cross the Oudezijds Achterburgwal, a canal in a busy district of Amsterdam. Weighing over six tonnes, the bridge was created using 3D printing. Now partners including The Alan Turing Institute are installing sensors on the bridge to turn it into a 'living laboratory', providing real-time information on its health during load tests.
The sensors collect data on structural measurements such as strain, displacement and vibration and measure environmental factors such as air quality and temperature, enabling engineers to measure the bridge’s health in real time and monitor how it changes over its lifespan. The bridge is thus a living laboratory for data scientists. Everyone that walks, runs, or cycles over the bridge will generate data about the behaviour of the structure.
The data from the sensors will be inputted into a ‘digital twin’ of the bridge, a living computer model which will imitate the physical bridge with growing accuracy in real time as the data comes in. The performance and behaviour of the physical bridge can be tested against its digital twin, which will provide valuable insights to inform designs for future 3D printed metallic structures. It will also enable the current 3D bridge to be modified to suit any required changes in use, ensuring it is safe and secure for pedestrians.
This digital twin technology could be used to virtually test all bridge designs that use 3D fabrication or algorithmic design technologies.
Professor Mark Girolami, Director of the Turing-Lloyd’s Register Foundation Programme for Data-Centric Engineering, said:
“The 3D bridge being installed by the MX3D team will be a world first in engineering. This data-centric, multidisciplinary approach to capturing the bridge’s data will also mark a step-change in the way bridges are designed, constructed, and managed, generating valuable insights for the next generation of bridges and other major public structures.
“3D printing is poised to become a major player in engineering, and we need to develop novel data-centric approaches for testing and monitoring to realise its full potential. When we couple 3D printing with digital twin technology, we can then accelerate the infrastructure design process, ensuring that we design optimal and efficient structures with respect to environmental impact, architectural freedom and manufacturing costs.”
This project will also impact the evolution and public awareness of bridge health monitoring, which, despite its importance, is not yet widespread. While the need for constant and effective monitoring is undeniable, it is still considered an accessory activity. The Smart Bridge will pioneer future structural health monitoring systems by providing an open-source example of active and self-managing safety systems.
The full span of the bridge was completed in 2018, and in 2019 the bridge passed the final load test. Gijs van der Velden, from MX3D, says: “Additional tests have been performed by the city in April 2021 on the ancient canal wall with promising results, so placement of the bridge is expected to take place this summer”.